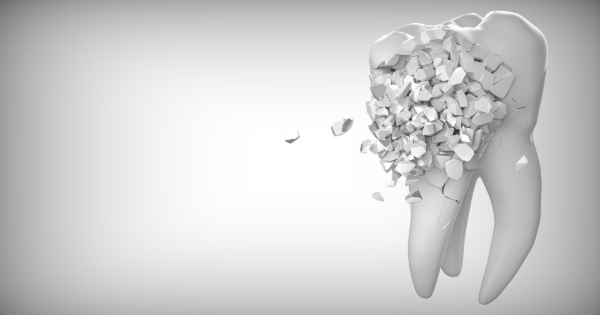
At Valley Orthodontic Laboratory in Snohomish, Washington, dentists who order mouth guards don’t get them through any old production method. For the last three years, the plastic guards have been made using the latest 3D printing technology.
Owner Jim Beierle still remembers the day a sales rep walked into Valley Orthodontic and presented him with what appeared to be an average night guard. Once the rep revealed that it had been made on a 3D printer, Beierle knew it was the alternative his family’s business needed to making mouth guards by hand. He soon invested $100,000 in 3D printers and scanners for the laboratory.
Beierle was more than a bit concerned after initially making this hefty investment. He only made 14 dental devices with the new equipment during the first month with it. Soon after, however, an increasing number of dental professionals in the area began adding digital scanners to their practices to create virtual 3D models of patients’ teeth and gums and send them to Beierle’s laboratory. Today, Valley Orthodontic prints 200 dental devices and night guards every month.
“The equipment paid for itself in the first year,” Beierle said.
Before this technology, patients needed to bite down on a mouthful of dental putty for about 20 minutes to create a mold of their mouth. This mold was then sent off to a laboratory to make custom mouth guards, retainers, and braces. With 99.7% of adults agreeing that having a healthy smile is socially important, these products are critical for helping people feel confident in their smile.
Depending on whether the lab was in-house at the dental practice or at a separate location like Valley Orthodontics, it would take days or weeks for the patient to receive their dental appliance. As putty molds aren’t completely accurate, the final product would typically need further adjustments for a perfect fit.
3D printing allows these appliances to be made in a matter of hours. In the case of braces, orthodontists can even scan a patient’s mouth beforehand and have a retainer ready for them the day that the braces come off.
This technology can be used for other aspects of dentistry as well. Patients who experience tooth decay or gum disease, which results from plaque that turns into tartar within the first 24 to 72 hours, often need dental crowns to replace their affected teeth.
Rather than waiting weeks for a perfect dental implant or crown, a dentist can use a 3D rendering wand to scan a patient’s mouth and then program their printer to make the right replacement all within the same appointment. This significantly shorter delivery time can make all the difference in a patient’s day-to-day life and confidence in their smile. And with 47.2% of adults over the age of 30 living with some form of periodontal disease that may require restorative dental crowns, there is certainly a patient demand for the fast-working technology.
Larger companies are starting to take notice of the technology as well. SmileDirectClub, the direct-to-consumer orthodontics company, is partnering with HP to develop 3D printed teeth molds. According to reports, SmileDirectClub will make over 50,000 unique mouth molds per day with 49 HP Jet Fusion 3D printing systems. With over half a million customers in the United States, Canada, and Puerto Rico, SmileDirectClub is hoping that this technology will help them keep pace with its rapid growth.
The companies also have a plan for sustainability in regards to their plastics production. In general, just 90% of plastic products are only used once. They then make their way into the world’s ever-expanding landfills or even its delicate oceanic ecosystems.
According to their plan, HP will recycle any excess 3D materials and plastic mouth molds that have already been processed to turn them into pellets for traditional injection molding. With the annual global production for just polyethylene, the most common plastic, at about 80 million tons, this sustainable effort will help mitigate the partnership’s effect on the planet.
These developments in both local businesses and large corporations are contributing to the continuous growth of this market. And there are technological innovations in many other sectors of the health industry, as well. For example, a laser hair removal session can take as little as 30 minutes. And the dental 3D market is growing even more rapidly. According to projections from research firm Transparency Market Research, the global dental 3D printing market is going to reach a value of $3.4 billion by 2025.
The technology is also being utilized in the automotive, industrial, and healthcare markets. While 3D printing won’t be able to replace necessary healthy practices such as eating at least five portions of fruits and vegetables every day, it has the potential to change surgical procedures, medical devices, prosthetics, and so much more.